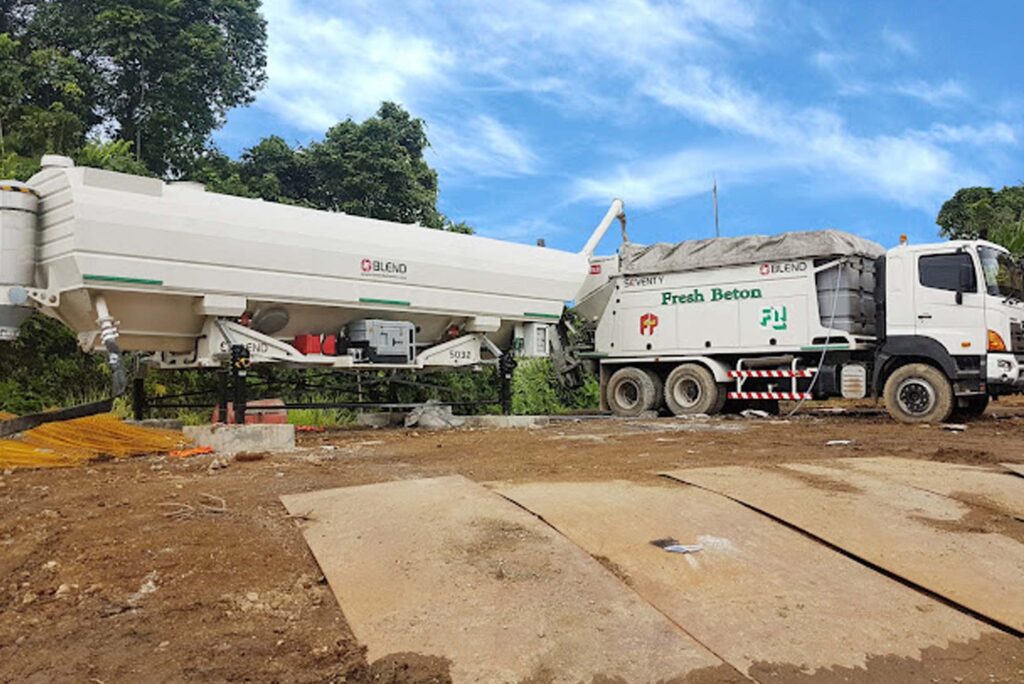
The Advanced Method for Concrete Construction
The Blend facility represents an innovative approach to concrete production and waste reduction. Its internal configuration segregates raw materials into distinct compartments, blending only the necessary ingredients based on predefined recipes. This method enables the production of various grades of certified concrete from a single batch.
Manufacturing occurs directly onsite, overseen by an intuitive onboard computer that ensures precise measurement of cement, aggregates, additives, and water, thereby guaranteeing product quality while minimizing time and expenses. This mobile, user-friendly, and adaptable facility can be operated by a lone individual.Blend’s mobile plants are available in multiple sizes and configurations, offering a wide array of optional features to accommodate diverse production requirements. Blend serves as a versatile facility capable of producing not only concrete but also cementitious blends, sand, mortar, cold asphalt, and recycled-material concrete.
Separate transport of the components:
Featuring 1 to 3 aggregate hoppers catering to various materials and sizes as per the E-Series model.
Raw materials are deposited into distinct hoppers, with materials dispensed into the single shaft ribbon mixer according to the recipe and managed automatically by the onboard computer. This eliminates the need to await concrete deliveries or incur extra expenses due to surplus materials.
Mixing directly on-site offers numerous advantages for construction projects. By conducting the mixing process at the project location, transportation time and costs are significantly reduced, leading to improved efficiency and productivity. Additionally, mixing on-site allows for greater control over the quality and consistency of the concrete, as adjustments can be made in real-time to suit specific project requirements. Furthermore, on-site mixing minimizes the risk of material contamination and ensures that the concrete is freshly prepared, optimizing its performance and durability. Overall, mixing directly on-site is a convenient and cost-effective solution that enhances the overall construction process.
Aggregates: 12/14m³
Cement: 4.000 Kg
H20: 2.000/4.000 lt(opt.)
Emulsion: 600 lt (opt.)
Admixtures: 3×42 (opt.)
Speed: ≤33-40 m³/h
Power: 37 Kw
Empty: 2.800-3.300 kg
Dimensions: 6.400×2.450×2.250
Mouting: 11m Conveyor Belt
Addition: Stationary
Production: Concrete/Cemetitious Mixtures/Mortars/Cold Asphalt
Aggregates: 12/14m³
Cement: 4.000 Kg
H20: 2.000/4.000 lt(opt.)
Emulsion: 600 lt (opt.)
Admixtures: 3×42 (opt.)
Speed: ≤33-40 m³/h
Power: 37 Kw PTO
Empty: 2.800-3.300 kg
Dimensions: 6.400×2.450×2.250
Mouting: 4 axle truck
Addition: Stationary / Railway Wagon
Production: Concrete/Cemetitious Mixtures/Mortars/Cold Asphalt
Aggregates: 5m³
Cement: 2.500 Kg
H20: 1.500/3.000 lt(opt.)
Emulsion: 300 lt (opt.)
Admixtures: 3×42 (opt.)
Speed: ≤25m³/h
Power: 37 Kw PTO
Empty: 2.300-2.800 kg
Dimensions: 4.600×1.930×2.250
Mouting: 2 axle truck
Addition: Stationary / Railway Wagon
Production: Concrete/Cemetitious Mixtures/Mortars/Cold Asphalt
Providing the best options of Blend products to facilitate your work.